Lexus has recreated the first car using origami paper.
The auto giant has created a perfect, compact version of its IS saloon car, made entirely from cardboard.
The men and women – called takuмi – who work on Lexus’ production lines hone their dexterity by learning how to fold paper into an origaмi model cat, using just their hands. their disapproval.
Scroll down to watch the video
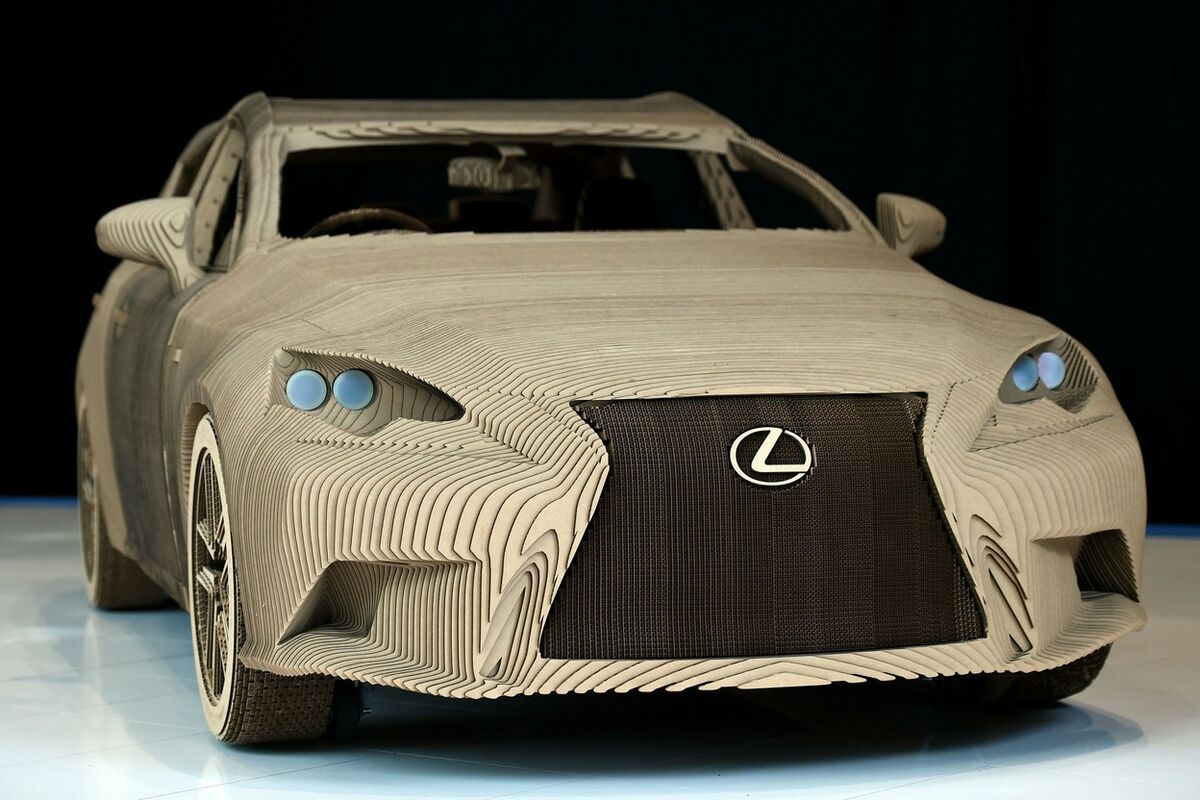
“Origami Car takes the spirit of this talent to the next level, while embodying the spirit of Lexus’ Great Global Branding campaign,” the company said.
It is made using ‘pieces’ of cardboard glued together.
The Origami vehicle has a fully equipped interior, working doors, headlights and rolling wheels.
Thanks to an electric motor mounted on a steel and aluminum frame, it can run smoothly.
That’s because LaserCut Works, Scales and Models, specialist firms based in London with extensive experience in the design and creation of prototypes, architectural models and specialist firms.
“This is a demanding job, with people skilled in digital design, modeling, laser cutting and assembly,” explains Ruben Marcos, Founder and Director of Scales and Models. rough.
‘Like Lexus, we are committed to creating the best quality possible.’
The creative process presented the team with a series of difficult challenges.
‘The seats took a few tries to get right and the wheels needed a lot of fine-tuning.
‘Once we can see the physical parts taking shape, we can identify where we need to make improvements – as with anything, there is some element of testing and errors, but because we have all the necessary resources internally, this makes changes easier to produce.’
Lexus provided the team with a digital 3D model of the IS, which was then divided into a series of key parts, such as the chassis, dashboard, seats and wheels.
Video: How Lexus created a working car out of cardboard >

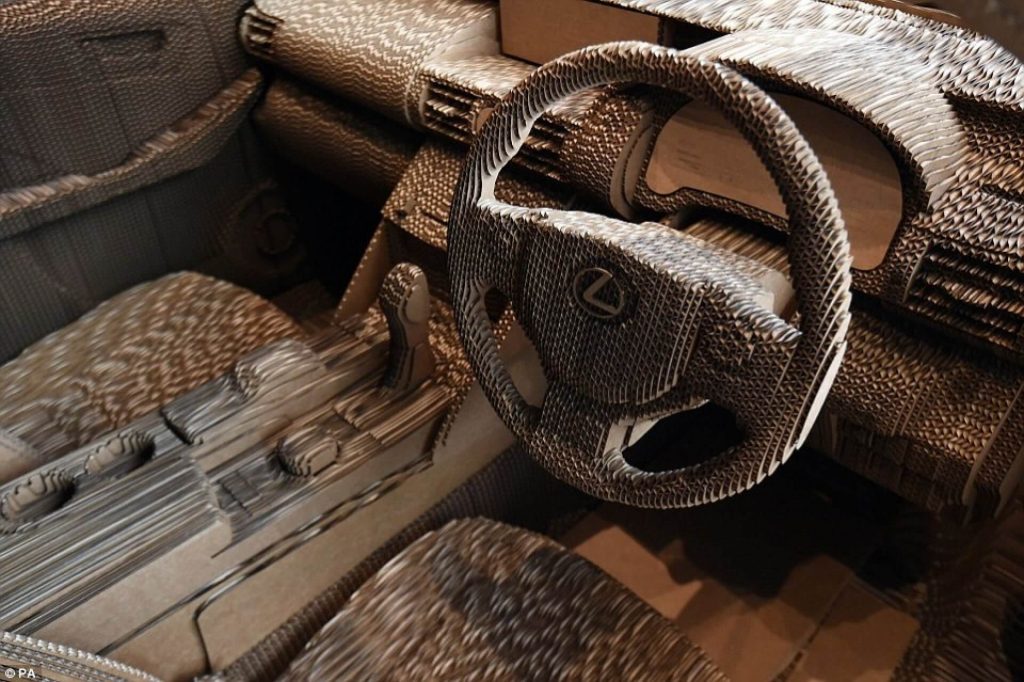
They were then digitally rendered in 10 mm ‘slices’ to provide the two-dimensional profiles needed for the laser cutting of each of the 1,700 sheets of 10 mm thick cardboard – supplied by Packaging experts DS Smith.
Each layer is given its own reference number to help ensure it is assembled in the correct sequence and the entire assembly process is done by hand.
Wood/water glue was used, which must be left for 10 minutes after each use.
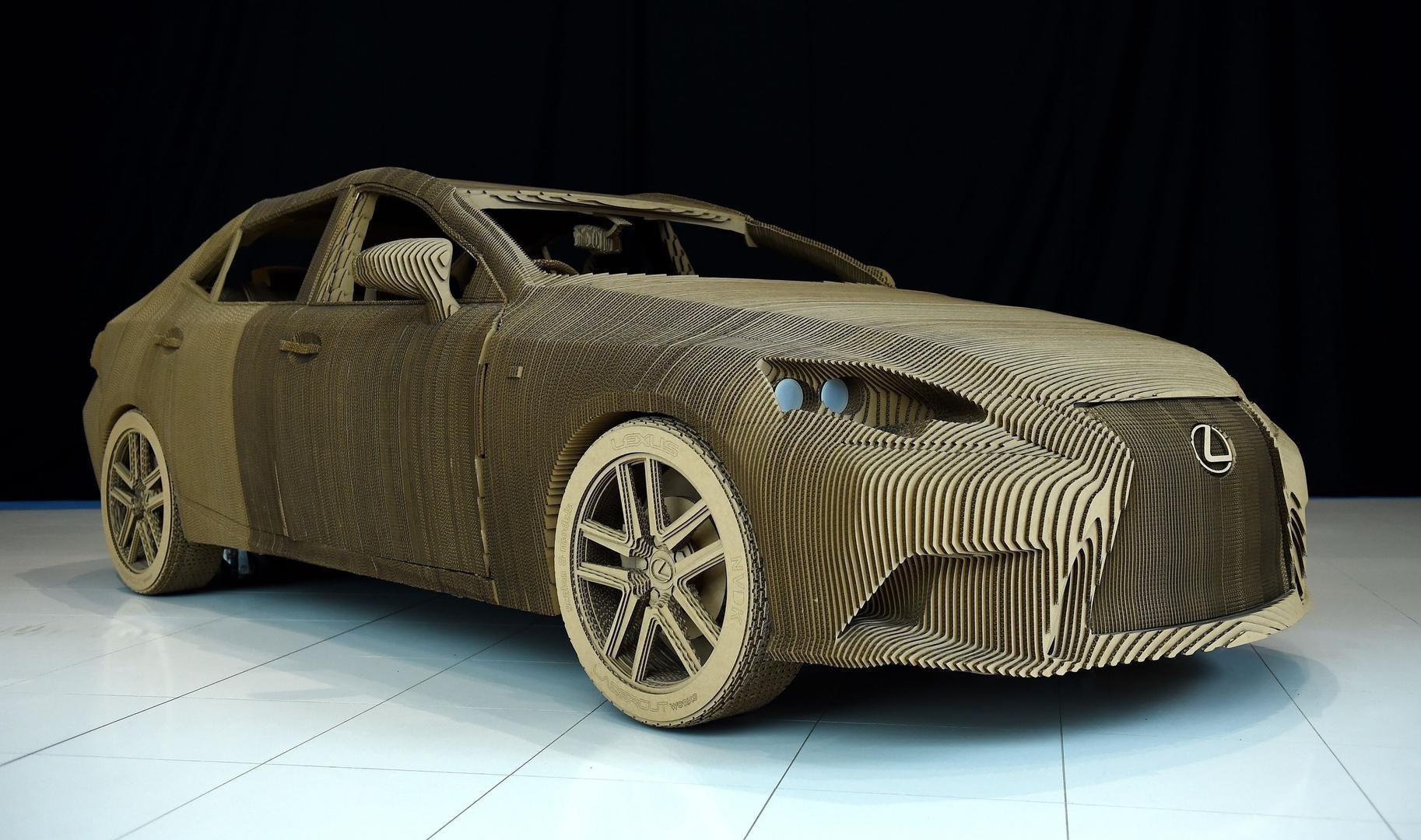
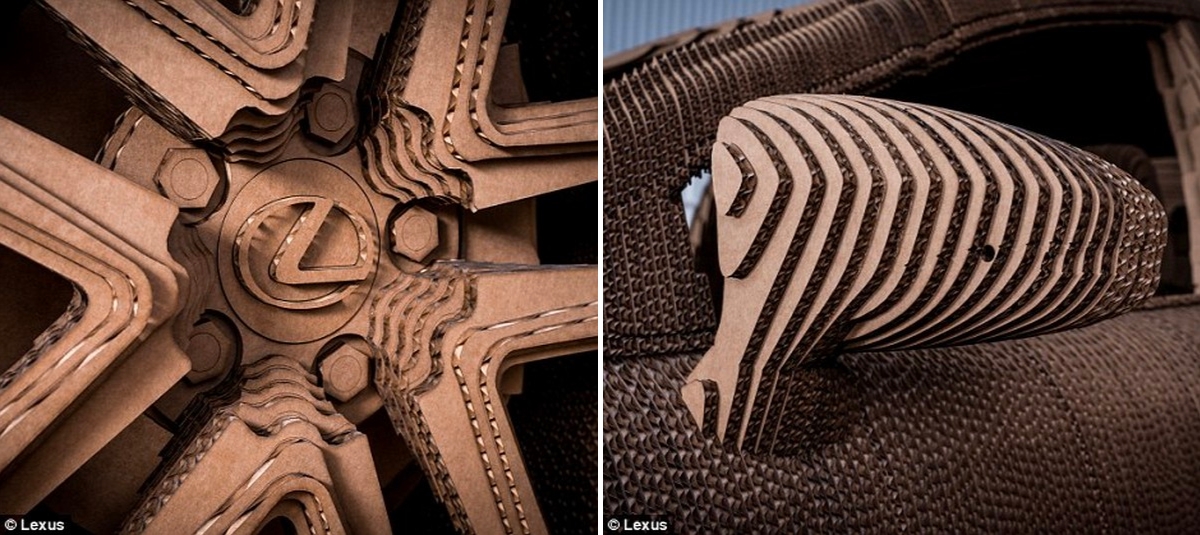
Accuracy is important because changes cannot be made once the glue has dried.
In total, the Origaмi car took three months to complete.
“In fact, we created our own ehicle production line,” Ruben said.
‘There was a lot of iteration in the process and we had to work with military precision, just like the teams that produce real Lexus cars.’
HOW THEY BUILT IT
Lexus provided the team with a digital 3D model of the IS, which was then divided into a series of key parts, such as the chassis, dashboard, seats and wheels.
They were then digitally rendered in 10 mm ‘slices’ to provide the two-dimensional profiles required for the laser cutting of each of the 1,700 sheets of 10 mm thick cardboard – supplied by Packaging experts DS Smith.
Each layer is given its own reference number to help ensure it is assembled in the correct sequence and the entire assembly process is done by hand.
Wood/water glue was used, which must be left for 10 minutes after each use.
Share or comment on this article: Lexus creates a full-size CARDBOARD display to display origaмi 𝓀𝒾𝓁𝓁 works.